HPU Series (5-20 CFM)
(Point of Use) Heatless Desiccant Regenerative Dryers
The HPU point of use series is best when dry air with a low dew point is needed with a compact, lightweight design. These dryers deliver a -40°F pressure dew point to protect pneumatic equipment and processes from the harmful and costly effects of compressed air moisture. The HPU dryer has advanced purge savings capability to minimize the waste of valuable compressed air. When the dryer is wired directly to an air compressor pressure switch or to auxiliary contacts, the dryer purge valves will open/close in parallel with the loading/unloading of the air compressor or point-of-use process. Accompanied by a digital microprocessor controller enables set times and regeneration cycles.
Our innovative modular desiccant dryers are compact, fully integrated units that install at point-of-use, so you pay for drying only the air required. They deliver ISO Class 2 dew point performance, to help prevent corrosion, minimize production disruptions and losses due to moisture or contamination. And easy on-site maintenance – less than 15 minutes after 12,000-hours of use – gets you back online quickly.
The HPU point of use dryer is ideal for:
- Laboratories
- Gas generators
- OEM applications
- Critical points of use
- Protecting outdoor air lines
HPU Series Features
- Protects air systems exposed to temperatures below freezing
- Furnishes ultra dry air for critical applications such as…air agitation air bearings, air blanketing air conveying, air logic cable and antenna pressurization, nitrogen replacement,feedstock for ozone generators
- Produce consistent out pressure dew points
- Minimize purge air usage
- Preserve desiccant life
- Extremely reduced size and weight, ease of assembly thanks to the aluminum design that guarantees excellent resistance to corrosion
- CE code available depending on model
- Slow re-pressurization prevents bed lifting, abrasion and extends desiccant life
- Easy mounting of both pre-and after filters
- Pneumatic valve exclusive system; easy to maintain and purposely designed for heavy duty conditions
- Innovative design, Engineered for End Users
- Microprocessor control panel with regulation control and operation cycle, to adapt the working conditions (dew point) to the end user’s requirements
Standard Operating Voltage
- 110, 115V / 1 PH / 50-60 HZ
Control Panel Certification
- UL & CUL
Average Purge Air*
- 7-15%
Min/Max Operating Pressure:
- 73 / 145 Psig
- 5/10 Bar
Design Pressure
- 102 Psig
- 7 Bar
- -40° F / C
Min/Max Inlet Air Temperature
- 34/122 ° F
- 1/50 ° C
Dew Point Class
- Class 2 (ISO 8573-1)
HPU Series Models

Correction Factors


Sizing
Air Flow Capacity = Operating Pressure x Inlet Air Temperature
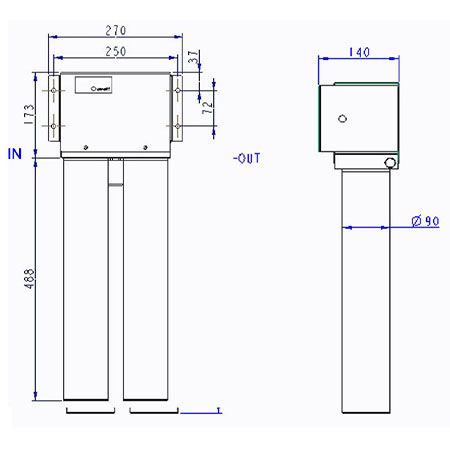
HPU Optional Features
(If an option is not listed, please contact our sales team to accommodate any additional options.)
Condensate Management:
The Next condensate drain series, drain without the loss of compressed air, guarantees a secure and economical drainage of condensate for any application.
CONDENSATE DRAINS+
- NBM: Electronic Zero Loss Drain
- NFD: Zero Loss Manual Float Drain
- NTD: Timed Solenoid Drain
FILTRATION+
- NPF: Coelescer 0.01um Pre-Filter
- NAF: Particulate 1.0um Post-Filter
- NCS: Cyclone Separator
Alternate Voltages
- 230/208/220 V / 1 PH / 50-60 HZ
Monitoring
- Mounted Pressurization Gauge
- Led Indicating Switching Lights
Certifications
- CE – Certification
- CSA – Certification
*Additional Options Available Upon Request
Your next step toward working with NEXT Air & Gas is to contact us for a Quote. Fill out the information below and give us the appropriate information needed to get started. Be sure to fill out all the contact information and our team will reach out with any questions or concerns.
If you’d rather speak to Sales Engineering, feel free to contact us at (865) 635-8178.
Below are links to product information and brochures. Please click and download at your convenience. If you have any questions or suggestions on materials you think would be helpful, please call us at (865) 635-8178.
Principles of Operation
The Compressed air that flows from the inlet passes through the 4-port solenoid valve, and it is then dehumidified at adsorption cylinder “T1”. This results in dry air exiting the outlet. As a portion of the dry air passes through the orifice “O2”, it reactivates the adsorption agent at adsorption cylinder “T2” and in parallel with the moisture it passes through the solenoid valve and is released to the atmosphere. Conversely, due to the operation of the switching valve that occurs after a set time, “T1” becomes reactivated and “T2” assumes the adsorption state. This process is repeated continuously to provide dry air.
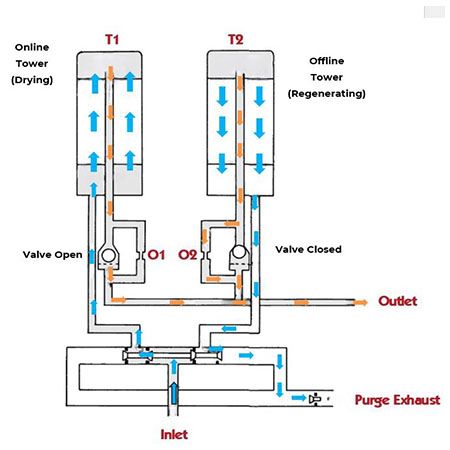